Packaging machine repair service for affordable maintenance solutions.
Packaging machine repair service for affordable maintenance solutions.
Blog Article
Why Timely Packaging Machine Repair Service Solutions Are Crucial for Operational Effectiveness
In the affordable landscape of manufacturing, the function of timely packaging maker repair services can not be overstated. Such solutions are essential not just for minimizing unintended downtime but also for promoting a smooth manufacturing environment that satisfies customer needs. By resolving small malfunctions before they intensify, companies can considerably boost operational efficiency and decrease long-term expenses. The implications of disregarding these solutions expand beyond immediate repair work, elevating concerns concerning devices reliability and total productivity. What techniques can business carry out to ensure they remain positive in their upkeep method?
Influence of Downtime on Manufacturing
Downtime in manufacturing can be likened to a ship adrift at sea; without a trustworthy training course, manufacturing processes can swiftly divert off track. The influence of downtime, specifically in packaging operations, can be both immediate and far-reaching. When equipment malfunctions, production halts, leading to a stockpile of orders that can stress customer connections and track record. Each min lost translates into earnings loss, as firms battle to satisfy market need and accomplish commitments.
Furthermore, unintended downtime interferes with process, leading to ineffectiveness that reverberate throughout the supply chain. Employees may be left still, causing decreased morale and productivity. Furthermore, the expense of emergency repairs usually exceeds that of scheduled maintenance, more stressing monetary resources.
In a competitive landscape, where time-to-market is important, the capability to preserve consistent manufacturing degrees becomes extremely important. Downtime not just affects prompt result yet can additionally develop a causal sequence that affects inventory levels, capital, and total operational effectiveness - packaging machine repair service. Therefore, understanding and minimizing the impact of downtime is vital for suppliers aiming to sustain their one-upmanship and ensure long-term development
Benefits of Regular Upkeep
Routine upkeep of packaging equipments works as an essential column in ensuring nonstop production and functional performance. By carrying out a regular upkeep schedule, organizations can significantly improve the dependability and durability of their tools. Regular inspections enable for the prompt recognition of deterioration, avoiding minor concerns from intensifying right into significant malfunctions.
Moreover, regular maintenance enhances maker efficiency, guaranteeing that packaging procedures run at peak effectiveness. This optimization not just boosts throughput yet additionally decreases the likelihood of product issues, thus keeping premium criteria. Well-kept machines add to energy efficiency, decreasing operational expenses linked with extreme energy consumption.
Along with efficiency benefits, normal maintenance promotes a much safer working setting. By More about the author making certain that equipments operate appropriately, the danger of crashes and injuries caused by tools failure is significantly decreased. This dedication to safety like this and security not just secures staff members however also aligns with regulatory conformity, minimizing potential lawful obligations.
Ultimately, buying regular upkeep enhances total productivity, reduces unexpected downtime, and promotes a culture of aggressive possession monitoring. This critical method makes certain that product packaging operations remain competitive in a hectic market, which is vital for continual success.
Cost Implications of Delayed Repair Services
Neglecting timely fixings on product packaging machines can bring about substantial economic consequences for services. When equipment malfunctions, manufacturing lines can stop, causing lost outcome and postponed delivery schedules. packaging machine repair service. Each hour of downtime translates right into not just shed sales however likewise potential fines from customers due to unmet due dates
Furthermore, postponed fixings can worsen existing concerns, leading to extra extreme damages and increased fixing prices in time. A minor malfunction can intensify right into a major break down, demanding pricey components substitute or a complete overhaul of the maker. This can strain budget plans and draw away funds this article from other vital locations, impeding general functional development.
Furthermore, businesses may face raised labor costs as workers remain idle or are reassigned during extended repair service durations. The longer machinery runs out solution, the extra substantial the effect on workforce productivity.
Enhancing Devices Longevity
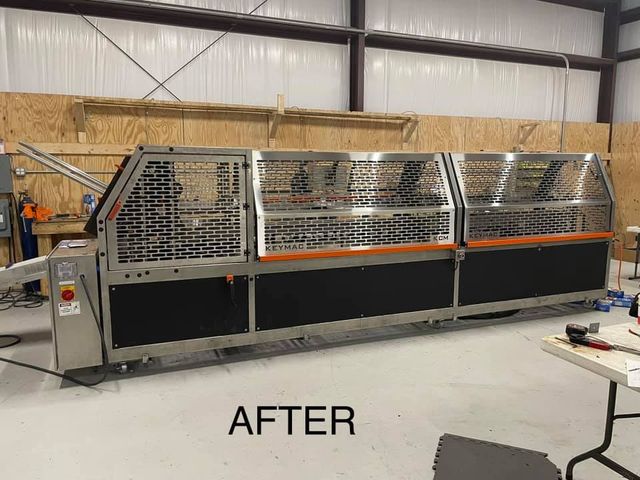
Carrying out a routine upkeep timetable can determine wear and tear early, stopping small concerns from escalating right into pricey break downs. This aggressive technique not only boosts the maker's functional integrity however also enhances the general manufacturing workflow. Operators needs to additionally guarantee that machines are used according to producer specifications to prevent excessive tension on critical elements.
Furthermore, buying high quality substitute parts during repair work contributes to devices long life (packaging machine repair service). Utilizing substandard elements might result in regular malfunctions, negating any expense savings understood from cheaper repair work. Correct training for operators on best methods for maker handling and procedure can also significantly impact the devices's life expectancy
Picking the Right Repair Service
Selecting the appropriate repair work service for packaging devices is necessary for ensuring minimal downtime and optimum performance. When evaluating prospective provider, consider their sector experience and field of expertise in packaging equipment. A business with a tested performance history in managing similar devices will likely possess the necessary know-how to detect and solve concerns efficiently.
Furthermore, assess the availability of technicians and their response time to service phone calls. A repair service that offers 24/7 assistance can dramatically reduce the influence of unanticipated equipment failings. In addition, make inquiries regarding their upkeep programs, as aggressive service can prevent pricey malfunctions and extend the lifespan of your equipment.
A reliable repair work solution should have a background of pleased customers who can confirm to their professionalism and trust and effectiveness. By thoroughly picking the best repair service, services can improve their functional performance and decrease interruptions in manufacturing.
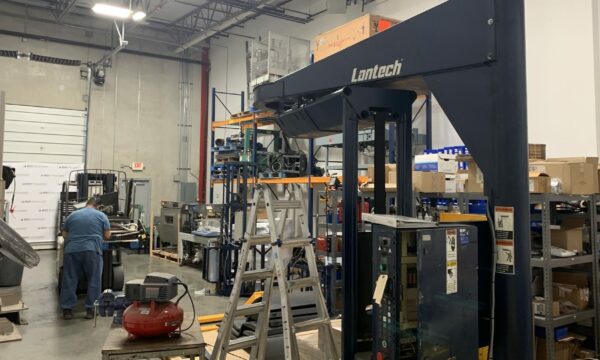
Final Thought
In verdict, prompt product packaging device repair work solutions play a vital role in preserving operational performance. Routine upkeep and prompt fixings offer to reduce minor concerns before they rise, thereby making certain ideal machine performance.
Report this page